More on Dip Coating
​
This is among the oldest and well known process for coating and thin film preparations, and have been used industrially for decades. It is advantageous for ensuring little or no material wastage. In this process, the substrate is dipped into a solution of the material of interest and later withdrawn at a fixed speed.
The process can be divided into several distinct parts
-
Immersion
-
Dwell time: this can be from a few seconds to several minutes in the case of chemical bath deposition*)
-
Withdrawal/deposition: the faster the substrate is withdrawn, the thicker the film)
-
Evaporation/drainage: Excess liquid drains from the surface of the substrate while the solvent in the deposit evaporates, leaving behind a solid film.
Depending on the solvent and solution viscosity, stages 3 and 4 can and usually do overlap.
Dip coating is a simple process for applying coating to even complex 3 D substrates without any complicated set up and is especially useful for layer-by-layer deposition, for example in the formation of hybrid (organic-inorganic) nano/micro-structure for sensors, catalysis and super liquid repellency (superhydrophobic or superoleophobic)
​
* Chemical bath deposition can be regarded as a form of dip coating in which only the dwell time matters, besides ambient conditions.
Applications
​
· Layer by layer/monlayer assembly
· Protective coating
· Complete coating on 3D objects
· Sol-gel
· Chemical bath deposition

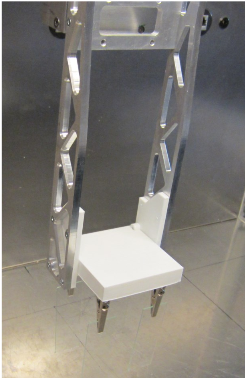