Modules





Technologies
Ultrasonic Spray coating
​
Dip Coating
​Inkjet printing
​
Electrospinning
​
Process automation
High thoughput experiments
​
Ultrasonic atomizer nozzle
Pick and place

Robotic platform
Rotator for tubes
UV light
Furnace
Ultrasonic atomizer nozzle
Products
The Multicoater combines all four important techniques into one robotic and modular platform, ensuring you do not need to install individual equipment for inkjet printing, electrospinning, (ultrasonic) spray coating and dip coating. It’s a matter of plug n play. You save on both cost and work space!
Often more than one thin film preparation process may be needed to complete your device and sample, and it can be a headache switching from one platform to another. Perhaps involving moving from one work bench or laboratory to another; from one environment to the other, for example from an inert environment at below room temperature to atmospheric conditions above room temperature. This can introduce uncertainty and unnecessary stress into your R&D. The Multicoater is designed to simplify your thin film preparation from solution processed materials, offering you the flexibility you need to realise your full potential in materials science and technology. All at a price that is the most competitive in the market – some competitors sell single process equipment, say electrospinning equipment, at the price of our system. Furthermore, the Multicoater can be customised to your specific need and is easily scaled up for pilot or industrial production
The usefulness of the MultiCoater to your R&D is enhanced by a selection of pre- and post-coating modules such as furnaces, UV lamp, driers, ultrasonic baths, automate chemical/material injection, and beaker racks. This allows the Multicoater to perform fully automated inline thin film fabrication.
We can Customise the system to address your specific needs, for example add a new module or have the dip coating set up to work as a chemical bath deposition platform.

MultiCoater
Two general configurations. In The left configuration the substrate is stationary and being coated by an ultrasonic nozzle, Inkjet nozzle, or electrospinning. In the dip coat setup, the substrate is being moved into the different modules. Allowing for process automation and high throughput setups. The substrate can be dipped in to a container or a spray.
Configurations
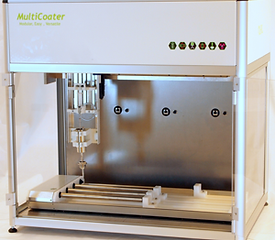
Ultrasonic nozzle and rotator module. For coating tubular substrates .
The software module is easy to use with sliders and numeric controls setting process parameters, such as length of tube, portion of tube to be coated, speed, flow rate and distance. Settings are easily saved and restored for recurring setups.
Spray coat configuration

Process auotomation
One of the Multicoater`s many innovations is the pick and place module. This module opens up possibilities of process automation, high throughput experiments and automated thin film production as an off the shelf solution. LRC offers Customs solutions and the system is scalable for industrial applications

Explore the unique properties of the inkjet technology, found in a desktop printers. With plug and play functionality, it’s easy to coat flat and tubular substrates. Small and dimensionally accurate coatings can be made without the need for masking
